Bulk carriers make up around 21 percent of today’s merchant ships. They are special ships used to transport solid bulk cargo, defined by the International Maritime Solid Bulk Cargoes (IMSBC) Code as “any cargo, other than liquid or gas, consisting of a combination of particles, granules or any larger pieces of material generally uniform in composition, which is loaded directly into the cargo spaces of a ship without any intermediate form of containment.” Some of the most commonly transported solid bulk cargoes include ore, coal, bauxite, phosphate, cement and grain.
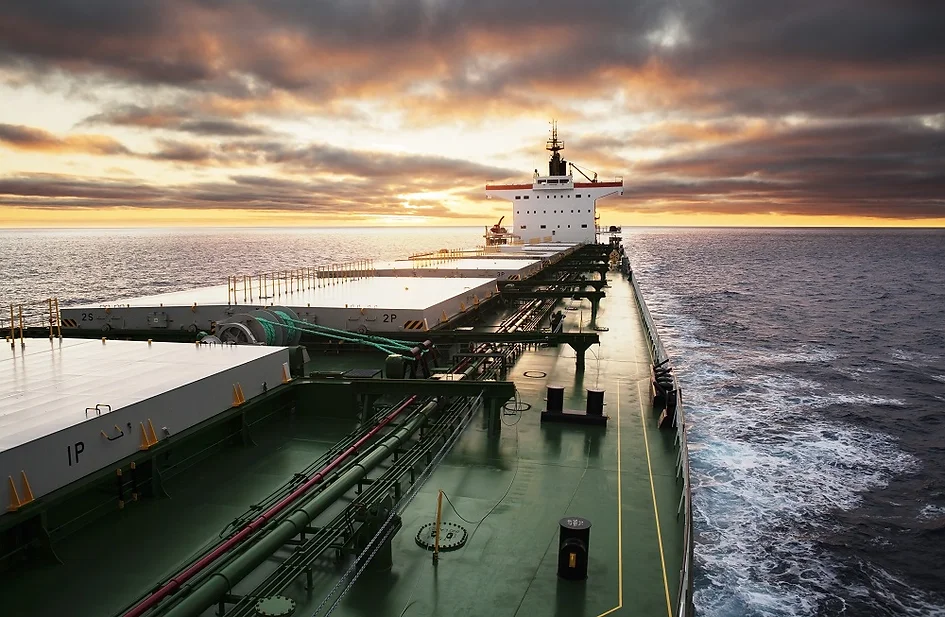
The solid cargo is directly loaded into the holds of the ship and is often transported thousands of miles across the oceans. While at first glance all this seems safe compared to dealing with liquid chemicals or oil and gas, this seemingly stable and dry cargo may turn from solid to liquid in a few minutes and cause a giant ship to capsize with no warning. This phenomenon is known as liquefaction and has been the cause for the sinking of approximately ten bulk carriers per year for the past ten years. To name a few, in January 2015 the MV Bulk Jupiter sank off the coast of Vietnam, carrying 46,400 tons of bauxite. In August 2013, the MV Trans Summer sank near Hong Kong, carrying 57,000 tons of nickel ore. Just a few months earlier, the MV Harita Bauxite sank in the South China Sea together with 47,450 tons of nickel ore. More recently, in October 2017, the bulk carrier MV Emerald Star sank off the coast of Okinawa in Japan, with 55,000 tons of nickel ore in the holds.
What exactly causes liquefaction?
Some solid bulk cargoes are more prone to liquefaction than others. In particular, some types of bauxite ores pose the highest danger. Bauxite ore is the main source of aluminum worldwide and around 100 million tons of this valuable raw material are transported by sea each year.

Certain forms of bauxite with a large proportion of smaller particles may tend to undergo a phenomenon called “dynamic separation”, in which the internal moisture in the particles is pushed out due to the pressure of the cargo, the movement of the ship and the vibrations from the engine. Pressure on the cargo is often increased as early as the loading stage, where solid cargo is often dropped into the holds from a relatively large height. The escaped moisture from the particles then forms a thin liquid slurry over the solid material, causing it to lose the friction that holds it still. The resulting free surface effect of the liquid (surge) can significantly affect the stability of a ship and even cause it to capsize.

The free surface effect occurs when tanks are only partially filled with liquids. For example, if a ship is sailing through rough seas, the liquid in the partially filled tanks will start to move due to the rolling of the ship. The liquid will flow in the direction of the heeling of the ship and will thus increase the already existing list, preventing the ship from righting itself. When this effect is not accounted for, and the cargo suddenly liquefies, the ship may lose its stability very rapidly. Other bulk cargoes prone to liquefaction are iron and nickel ores.
What can be done to prevent liquefaction?
In most cases liquefaction leads to loss of the entire ship, death of the crew, and environmental pollution. It is therefore of critical importance to prevent it from happening in the future.
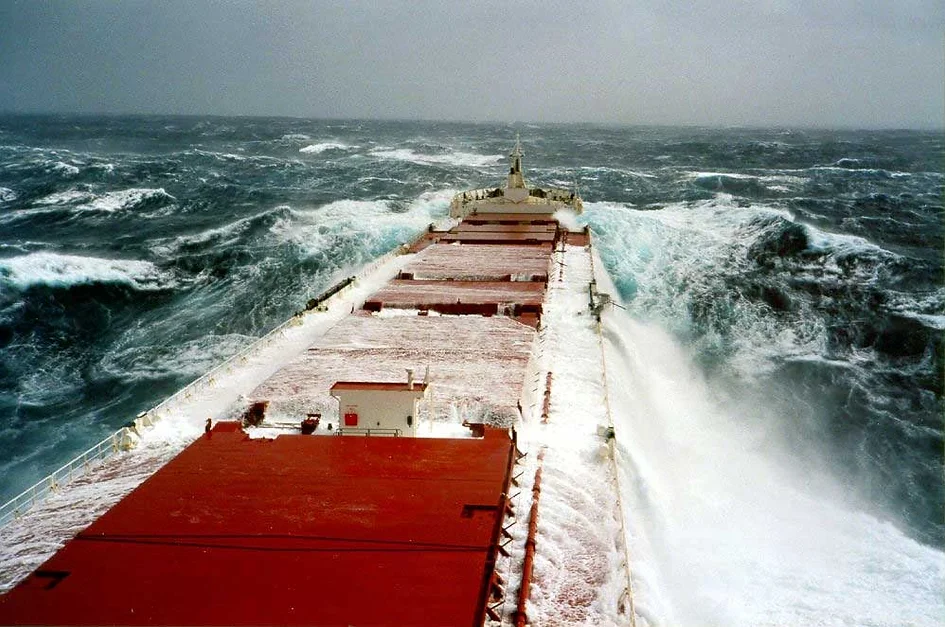
Safety regulations for bulk carriers specify a Transportable Moisture Limit (TML). This means that ores are tested for moisture before being loaded on the ship. Unfortunately, this is not always an effective safety measure, as the moisture content of the ore may change after it is loaded into the cargo holds. On-board tests can be done, where the ore is tested for moisture every so often during the voyage. However, samples are often taken using questionable methods and consequently lead to inaccurate results.
Besides, moisture is not the only factor involved. Liquefaction may also depend on particle size and distribution, density of the cargo, as well as loading speeds and methods. Cargo is often loaded rapidly using unsafe techniques in order to save costs.

Preventing liquefaction in the future will depend on stricter implementation of regulations for loading and testing of cargo, a better understanding of solid bulk cargo behavior, and on modern hold sensors to recognize liquefaction warning signs and alert the crew in time.
See you next time!
The Shipyard