Shortly put, cavitation is the formation and dissolution of vapor-filled voids (vapor bubbles) in liquid mediums. But how do these voids form when looking at cavitation in terms of ship propellers and what do they mean for the functioning of the propeller?
Because a ship’s propeller rotates through the water at an angle of attack, a pressure side and a suction side are created on each of the propeller’s blades. The faster the blades cut through the water, the lower the pressure on the suction side of the blades becomes. At a certain speed, the pressure on the suction side is so low that the water flowing over that area evaporates, forming vapor bubbles or voids. This happens because at “normal” air pressure of 1013.25 hPa, water evaporates at 100 ° C. At a higher pressure, the evaporation temperature is higher, and respectively lower at a lower pressure. Thus, in this case water starts boiling and evaporates at a pressure of 23.37 hPa at a temperature of 20 ° C.
Going into more detail, when the local pressure decreases below the vapor pressure, water evaporates, a cavitation bubble forms, grows larger and gets transported with the flow to a region with a higher pressure. At this point the bubble stops growing and when the local pressure exceeds the vapor pressure, vapor condenses starting from the wall of the bubble. Eventually, the surface of the bubble starts to break down in its weakest spot and the bubble implodes. During this implosion, the water flows back into the space to fill the collapsed void whereby pressure surges arise that can have orders of magnitude of several hundred MPa. This process creates pressure waves with high pressure peaks. If the vapor bubbles are in the vicinity or directly on top of a solid wall surface, such as propeller blades, the implosion produces a liquid microjet, which exerts high stresses onto the surface. The sudden release of energy causes pressure loads on the surface, which create crater-shaped material erosion in the propeller blades.

In addition to the erosion, the layer of bubbles packed onto the surface of the propeller blades makes them “thicker”. This increases resistance, as the blades move through the water, which in return decreases the performance of the propeller. Last but not least, cavitation can also cause loud popping noises and vibrations, which further affect ships and those travelling on them.
The main causes of cavitation are unevenness in the leading edge of a blade, too much curvature of the blade, excessive sharpness of blade edges, or poor finishing of the blade surfaces.
How Were the Causes of Cavitation Discovered?
While questions about the principles behind cavitation were already raised in 1754 by Leonhard Euler and later by Robert Edmund Froude, historians claim that cavitation was first physically observed by John Isaac Thornycroft and Sydney Walker Barnaby on the HMS Daring’s propeller in 1893. Barnaby joined efforts with Sir Charles Parsons, builder of the Turbinia, to further explore the assumption that it was tiny bubbles around the propeller that caused the HMS Daring to fail during her first sea trials. Two years later, the first cavitation experimental facilities were set up by Parsons to determine the exact relation between the formation of bubbles and the erosion in the propeller.
In the early 1900s, with the emergence of the Kaplan turbine, invented by the Austrian engineer Viktor Kaplan, the cavitation phenomenon became a major reason for concern when several Kaplan turbines were returned due to cavitation damage. By the 1920s Kaplan, already suffering from serious health issues, was desperate to fix the cavitation problem and appointed his assistant, Jaroslav Slavik, to continue his work in the laboratory.

The laboratory was set up in the basement of the German Technical University in Brno and sponsored by Ignaz Storek, owner of the Storek foundry and machine factories. With the help of Gustav Oplusstil, the company’s hydraulic operator and former frigate lieutenant of the navy, a small test turbine was installed next to a power plant in Iserthal, in order to observe the cavitation process. Oplusstil had previously observed similar occurrences, as those on the Kaplan turbines, on the propulsion propellers of the fleet’s fast-moving destroyers. While shipbuilders already knew that these were “cavitations”, they were not aware of the exact causes of the problem. Oplusstil and Slavik, together with other laboratories simultaneously working on the problem, were finally able to develop turbines that did not cavitate when properly installed.
While Kaplan and his team are often referred to as the ones who solved the problem of cavitation, it was actually John William Strutt, 3rd Baron of Rayleigh, in 1917, who came up with the equation that defined the collapse of an empty cavity in a large mass of liquid.
Preventing Cavitation
The ship’s hull influences the flow around the screw because the screw works fully in the ship’s wake. The phenomenon of cavitation plays a very decisive role in choosing the shape, material and operation of marine propellers. In order to avoid cavitation in slow ships, with speeds below about 35 knots, the propellers receive flat, so-called low loaded profiles with very small angles of attack. Multi-blade screws with large diameter and wider blades are needed to achieve sufficient overall thrust at low negative pressure or low pressure-differences. When designing such screws, it is particularly important to take into account the flow curvature along the screw surface. For reasons of strength, ship screws require more blade surface than air propellers, which adversely affects the circulation distribution, necessary for propulsion, around the blades.

In faster ships with speed over 40 knots, cavitation is almost unavoidable. Cavitation wear could potentially be prevented if a propeller is designed to always work at full cavitation, also known as supercavitation. Supercavitation utilizes cavitation principles to create a vapor void big enough to envelop a whole object moving through a fluid, therewith decreasing the drag on the object caused by friction. Reduction of hydrodynamic drag allows objects to travel through fluids at exceptionally high speeds. Experiments so far have confirmed the possibility to construct an efficient supercavitating ship propeller at speeds up to 80 knots.
Due to damage by cavitation and the aggressive nature of saltwater, ship propellers are usually made of Cu-Sn and Al-multi-material alloys (bronze) in high-load propellers (large blade pressure differential) or stainless steel (Cr> 13%) in high-performance propellers. Because high-load propellers have a large blade pressure difference, they require additional measures to reduce the impact of cavitation. Material accumulation and/or air supply are carried out at the cavitation-prone areas. The air is supplied through lines mounted in the shaft and from there it passes through channels in the blades, until it reaches the surface of the blades where it exits through specially drilled holes.
Supercavitation – How to use Cavitation as an Advantage
Using the principles of cavitation, an object or a certain area of the object moving through water can be purposefully enclosed in a bubble. As already mentioned above, the bubble then reduces the direct contact of the object with the water, resulting in lower hydrodynamic drag and allowing the object to move faster. The bubble is either created as a natural effect from the shape of the object travelling through the water or alternatively, through a gas source on the inside of the object.
First experiments with supercavitation took place during the 1940s in the Soviet Union. The concept was eventually applied to develop a supercavitating torpedo launched in 1977, known as the VA-111 Shkval. The Shkval was designed with a flat circular nose, resembling a disk. The edge of the flat disc caused water to swerve to the side, therewith creating a supercavitation bubble.
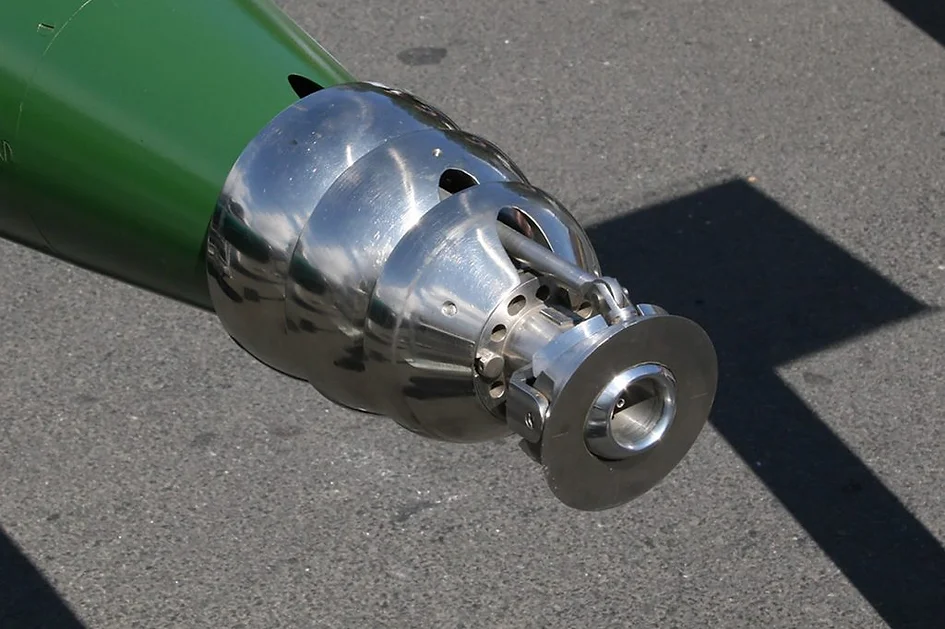
Since then, other attempts have been made to apply supercavitation to propellers, submarines, and ship hulls. Two major challenges have always stood in the way of past efforts, though: speed and maneuverability. In order to create such a bubble around the nose of the object, the object must already be travelling through the water at a certain minimum speed. An even higher speed, approximately 40 knots, needs to be maintained to keep the bubble from imploding, which is difficult to achieve in practice. Maneuvering the object further complicates implementation, since the traditional rudder of a ship or submarine is very likely to puncture the surface of the bubble. This would cause a sudden increase in frictional drag, or a collapse of the entire bubble, which at such high speeds could result in the rudder breaking off.

This is just a small overview of a complex phenomenon that has been around since the very beginning of turbines and srews. Have you got any personal stories to tell on the subject? I would love to read about them in the comments below!
P.S. If you have any photos showing the effects of cavitation that you would like to share, feel free to e-mail them to me and I will feature them in my Instagram feed!
The Shipyard